DCS Market Drivers Extract
DCS Market Drivers Extract
In a growing number of instances, the major DCS and PLC vendors now find themselves bidding on the same jobs, and PAC solutions are winning contracts that would previously have gone to DCSs. Examples of such “hybrid” applications might include a food processing plant, which in the past might have used a DCS at one end of the plant for the process control, and a PLC at the other end to handle the packaging line; this plant today might instead be using PAC technology to do the entire, integrated control job. The same kind of thing is happening in oil & gas, pharma, water/wastewater and other traditional DCS strongholds.
The overall discussion with end customers must be defined by the benefits of Automation Asset Management of a DCS based system versus a PLC based system, such as the Emerson Ovation DCS. These benefits better prepare a customer for Advanced Applications (Advanced Process Control, Optimization) and Production Management (Production Planning, Operations Management, Yield Accounting) and include:
- Reduced Life Cycle Cost through higher plant availability, increased personnel productivity and improved utilization of available capacity
- Improved Safety Performance through accurate and available documentation, work process and asset model information
- Improved Return on Asset Performance through asset visualization continuous improvement, risk management and disaster recovery
- Support for Regulatory Compliance through OSHA 1910.119 Process Safety Management, 21 CFR Part 11 Electronic Records & Signatures
- Cyber Security for automation assets and meeting Critical Infrastructure Plan (CIP) standards
The process control system is at the core of any automated process facility being managed; distributed control systems (DCSs) control the process directly together with integration of packaged process units having independent programmable logic controllers (PLCs). DCSs were built on proprietary protocols historically, but as the technology is reshaping very quickly and customers are becoming more demanding, the requirement of integrating everything (control systems) under one system (DCS) has become the key to success together with cost effectiveness, causing the DCS original equipment manufacturers (OEMs) to move towards more open systems. As the DCS has become open in terms of ease of integration with almost all types of systems, its lifecycle has decreased. There are several more reasons to upgrade a DCS or PLC based system. The most common factor in upgrades is the product’s end of life, which will push users to stock more operational spares in order to continue using the current DCS or PLC based system or buy refurbished hardware from the open market.
End of support
• The OEM stops providing support on old systems, or the level of support is reduced to the bare minimum, which pushes end users to upgrade.
Lack of knowledge
• Skilled resources are not easy to find especially when it comes to older or legacy systems. If there isn’t a specialist on-hand who is familiar with the old system, it may be time to consider replacing the existing system.
Performance issues
• Performance matters a lot. Obsolete or older hardware can’t perform to meet today’s needs and requirements.
Lack of openness for expansion or integration with newer systems
• It becomes very difficult to integrate new systems with older ones due to integration limitations.
Lack of features required for enhancing the control philosophies
• Process control techniques are always evolving and enhancing ways of optimizing the process and its efficiency. This requires newer functionalities in the systems to be used and implemented which either are not available in older systems or are very complex/difficult to implement.
Maintenance costs
• Maintaining older systems is always expensive whether it’s obsolete components, availability of specialists, or retention of older employees, and so on.
Paths to upgrade
• There are many paths that could be opted for by the end user while deciding on an upgrade. Most of the DCS OEMs have already designed their upgrade paths accordingly.
• One of the simplest approaches is to replace all of the existing DCSs at once—including all human-machine interfaces (HMIs), control hardware, and input/output (I/O) modules. This path might seem easier to deploy, but it has some factors like longer downtime, reduced efficiency of operational staff as they have to switch to newer systems in one go, and so on.
The most commonly used approach is upgrading in steps or phases.
Phase 1: Supervisory layer component upgrade
• Supervisory layer components involving HMIs and communication network elements between control systems and HMIs are upgraded in phase 1. This enables the end user to get familiar with the new system operationally. Having the old HMIs run in parallel with the new HMIs is beneficial because it gives the operators a chance to become familiar with the new system.
Phase 2: Control system upgrade (except I/O modules for some OEMs)
• Phase 2 involves upgrading DCS control hardware. This is a critical phase and has to be planned in more detail as compared to phase 1. It may involve downtime based on DCS configuration and upgrade limitations.
Phase 3: I/O modules upgrade [Optional]
• Phase 3 involves upgrading I/O modules and relevant hardware in a DCS. It may also involve downtime based on I/O module configuration and upgrade limitations.
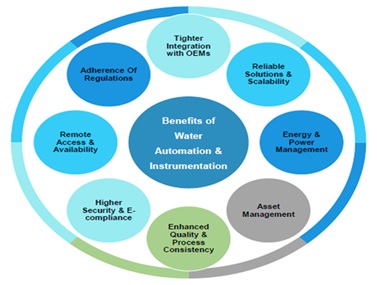
DCSBenefits
end
Tags: DCS Market Drivers,